When looking at a switch’s data or spec sheet, you’ve likely come across the term “contact resistance.” Well, what is contact resistance in a circuit?
The overall concept for the term is pretty basic. We’ll get into that, but first, what are contacts?
Contacts connect the flow of electricity between multiple devices. They can be found on a myriad of things such as switches, breakers, relays and much more. Contact resistance is just as it sounds: it’s the amount of resistance to the flow of electricity between one contact to another. So it refers to the resistance encountered at the point of electrical contact between two conductive materials.
In a circuit, electrical current flows through conductors, and when these conductors meet or make contact with each other, there’s potential for resistance at the contact interface. This resistance can result in energy loss in the form of heat.
Contact resistance is influenced by several factors, including the material properties of the conductors, surface roughness, cleanliness of the contact surfaces and the applied force between the contacts. The resistance at the contact point can vary based on these factors and can increase over time due to the surface conditions of the contacts — think dirt, rust or corrosion.
We can visualize this by imagining water flowing through a funnel, the water being the electrical current and the funnel the contacts. Water flows through easily with minimal resistance.
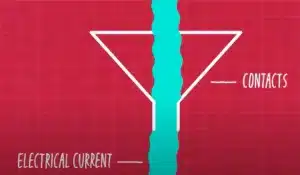
If we add another obstacle to the funnel, the flow of water has more resistance and slows down. If we add too many obstacles, the water will start to overflow.
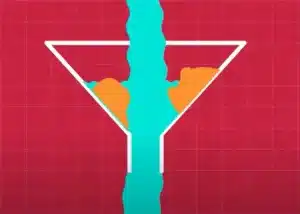
Low resistance is desirable in electrical circuits to minimize energy loss and ensure efficient current flow. High resistance can lead to voltage drops, heating at the contact points and degradation of electrical performance. In some applications, materials with low contact resistance — such as silver or gold — may be used to improve the overall efficiency and reliability of the electrical contacts.
It’s important to know contact resistance in order to maintain contacts and ensure proper use, especially when it comes to high current loads. For example, the contacts in your home circuit board should be checked periodically to ensure they’re functioning properly. Regular maintenance and cleaning of contact surfaces are common practices to reduce resistance and maintain optimal circuit performance.
Poorly maintained or damaged contacts could lead to arching. This is when a circuit becomes overloaded and the electrical current flows through the air from one conductor point to another. This could result in fire or an electric shock. This is obviously an extreme example, but it’s important to understand that throughout a switch’s life, resistance tends to go up. It’s only natural for silver contacts to slowly tarnish over time.
Typical vs Initial Contact Resistance
Now let’s take a look at how this is written in a data sheet. If we look at the specifications, this particular tact switch has a contact resistance of 50mΩ max initial @ 2-4 VDC.
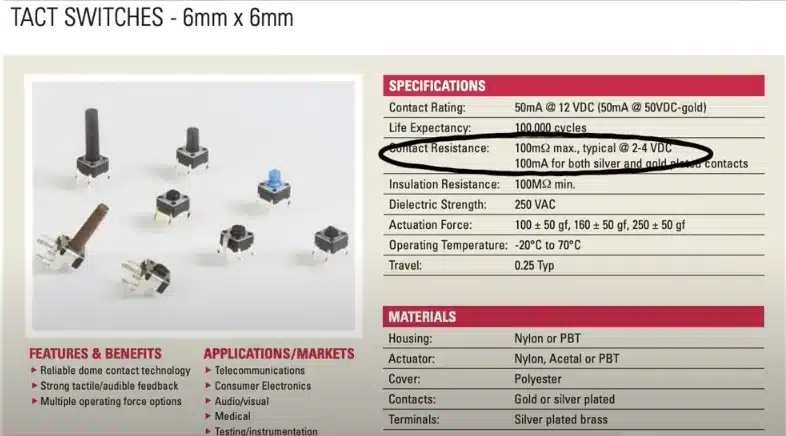
This one says 100mΩ max typical @ 2-4 VDC.
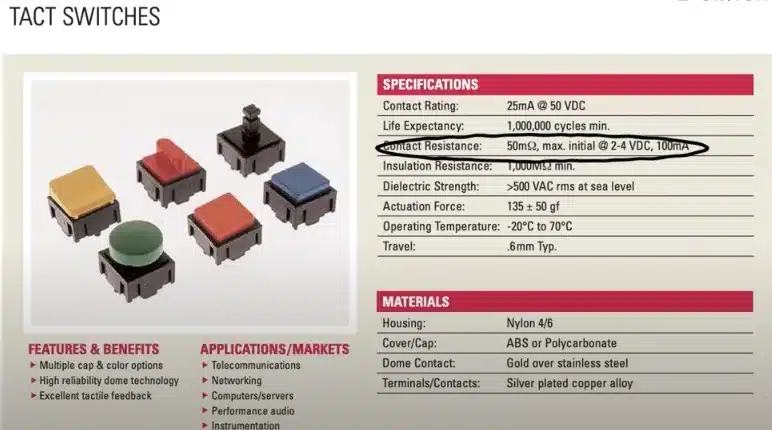
Because environmental conditions can play such a huge role in changes in contact resistance — like a high humidity area by the coast with increased salt in the air — the word “typical” is used to factor in these varying conditions and provide a typical resistance. “Initial,” on the other hand, refers to the brand new switch as it’s shipped out the factory door.
Overall, resistance varies depending on the type of switch and the application.